入社1、2年目のデータサイエンティストが、モノづくり現場の課題を解決に挑む。日立の「モノづくり実習」が熱い!
通信機器やセンシング技術の発達とともに、あらゆる分野でビッグデータが日々、生成・蓄積されています。それらをビジネスへと有効活用できる人財、いわゆるデータサイエンティストへの需要は高まるばかりです。
そんなデータサイエンティストの育成に早くから着目してきた株式会社日立製作所(以下、日立)は2020年3月に「Lumada Data Science Lab.(以下、LDSL)」と呼ばれる、デジタルイノベーションを加速させるAI・アナリティクス分野の中核組織を設立。同社が有する幅広い業種・業務の専門的知見やノウハウ、人財、先端技術を集結し掛け合わせることで、社会課題解決に向けた価値の創出を加速させています。
今回は、そんなLDSLが取り組む超実戦型現場研修「モノづくり実習」について、責任者および受講者・経験者となる入社1〜2年目の若手データサイエンティスト4名に、それぞれお話を伺いました。日立がもつ広範囲なOT(Operational Technology)を、データサイエンスの力でさらに昇華させていく企業文化の「胎動」を感じる内容となりました。
日立製作所経験者採用実施中!
AI/アナリティクス技術により顧客の課題解決を行うデータサイエンティスト
[Assistant Manager]
募集職種詳細はこちら
目次
プロフィール
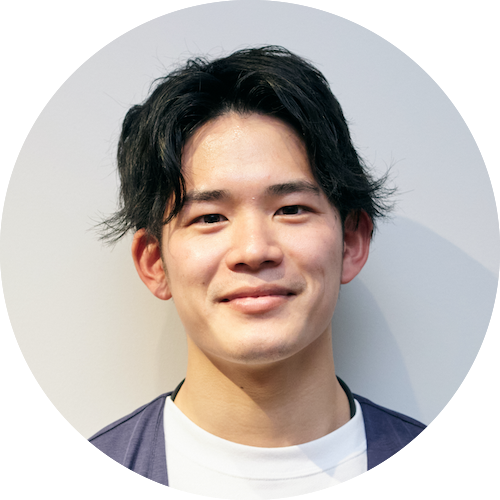
Lumada Data Science Lab.
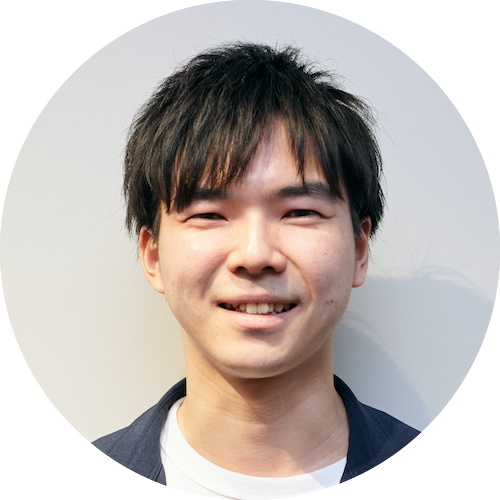
Lumada Data Science Lab.
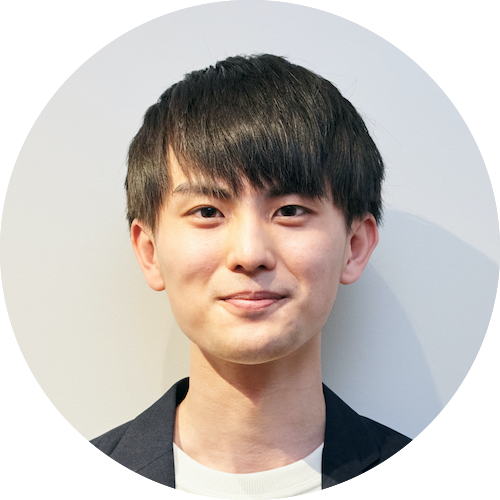
Lumada Data Science Lab.
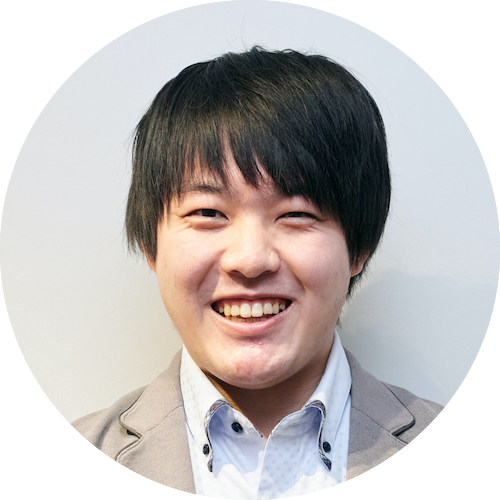
Lumada Data Science Lab.
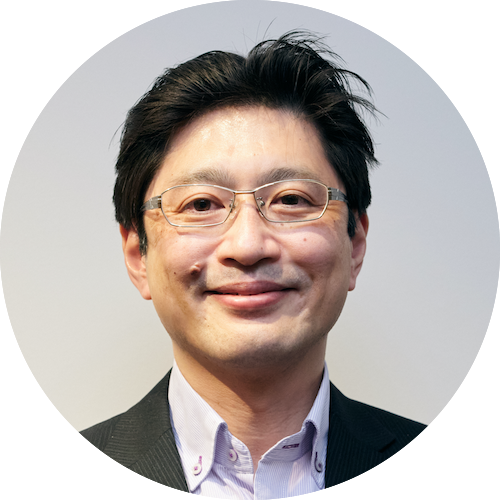
Lumada Data Science Lab.
実際の現場に入り込んで課題解決ができる「モノづくり実習」
――今回はLDSLが実施しているデータサイエンティストに向けた「モノづくり実習」についてということで、まずはこの研修の概要について教えてください。
徳永 : 「モノづくり実習」とは、モノづくり現場で行われるデータサイエンスの実習です。日立のモノづくり現場で実際に起こっている課題を自ら発見し、改善するプロセスを経験できるのがこのプログラムの最大の特徴、目的となっています。
よく「モノづくりは日本の屋台骨となる産業だ」と言われていますが、一方で現場のDXが進んでいないことが大きな課題になっています。様々な理由が考えられますが、現場の「課題の本質」をデータサイエンティストが理解できていないことが要因の1つとして挙げられます。現場課題を本質的に理解できていないから、現場との様々な合意がとれず、結果としてDXが思うように進まないというわけです。
これに対して、多様な領域でモノづくりをしている日立では、実際の現場に入り込んで課題解決ができる。まさに日立だからこそ実現可能な環境、プログラムとなっています。
――OTとITの両方に強みがあるからこそ実現できたプログラムということですね。
徳永 : 日立は、まさにその組み合わせ(OT × IT)を強みにもつソリューションビジネスを展開しています。だからこそ、ビジネスを進める上でもOTが何であるかを自ら語れるような経験をしてもらいたい。そんな人財育成の観点もありました。
モノづくり実習自体は従来から入社1年目の人財育成プログラムとして行っており、そこではデータサイエンティストもソフトウェアの開発工程やソリューション開発、提供などの実習を行っていました。
ですが、せっかく日立のデータサイエンティストとして入社したからには自身の力量を測る意味でも「分析に関わる経験」を積んでほしい。そこで昨年度より人財部門と連携して、モノづくり現場での実習の企画、運営を開始しました。
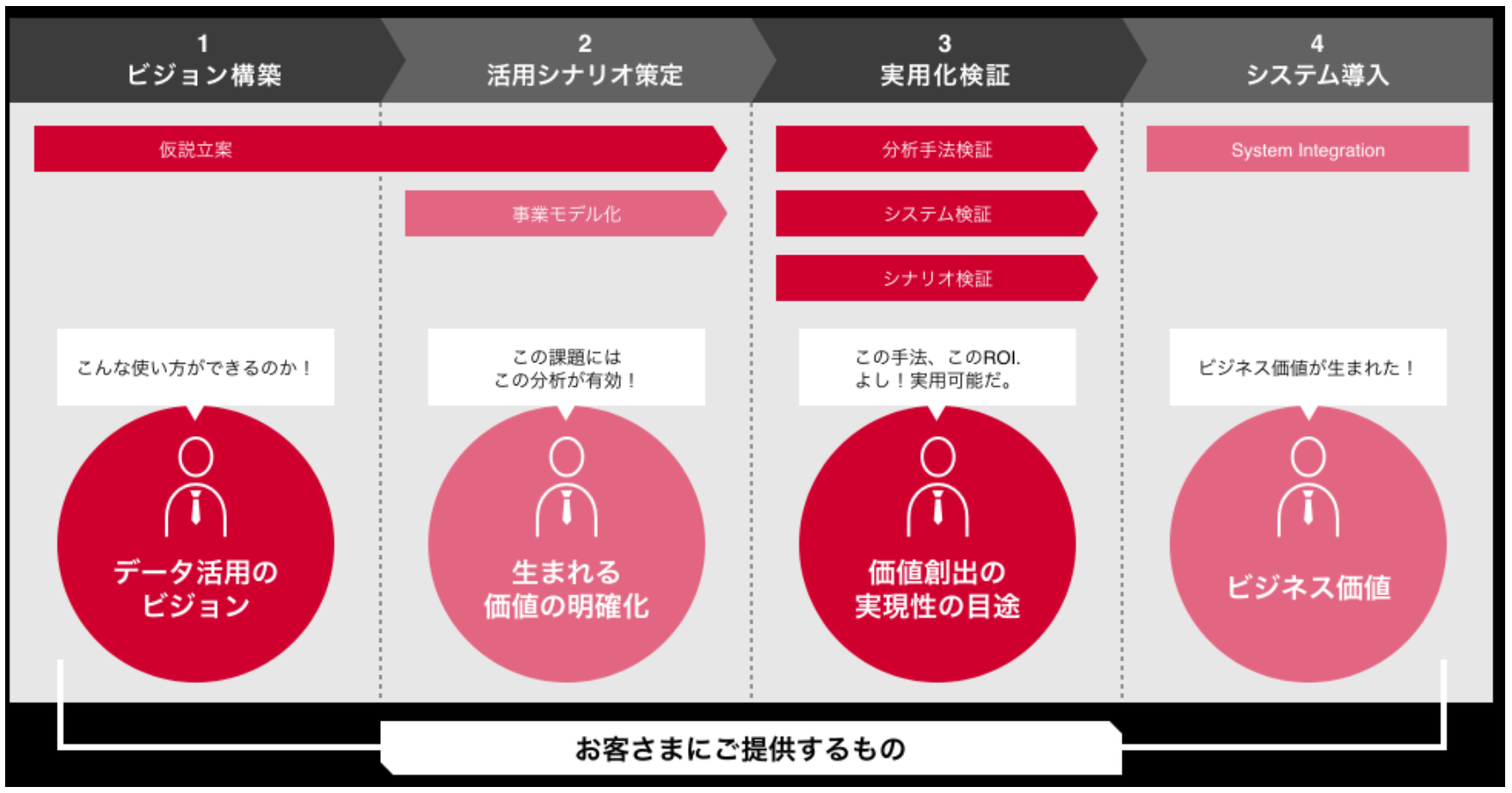
日立では、ビジョン構築からシステム導入まで、ビジネスに繋げるために必要となる様々な要素をコーディネートしプロジェクトをプロデュースすることがデータサイエンティストの役割だとして、各種研修や体制を整備している
――入社1年目が対象のプログラムなんですね。どれくらいの期間で行うのでしょうか?
徳永 : 3ヵ月間でDXを進めていきます。そのためには現場の課題をヒアリングし、それらをデータの裏付けを加えながら証明し、業務改善に向けて業務プロセスの変革を進めなければなりません。それには現場の皆さんに価値を認めていただくのはもちろん、IT部門との連携など、様々なステークホルダーとの信頼関係の構築が必要となります。また、日々の業務に負担をかけない方法で検証を進めるなど、人間力を高める訓練も必要です。つまり、データサイエンティストには分析力だけでなく、課題を特定する力やコミュニケーション力も必要なのです。そういった訓練を積み重ねることで、総合的な力を身につけ、一人前のデータサイエンティストが育成できると考えています。
入社2年目メンバーのケース(清水目さん・小幡さん)
――実際にモノづくり実習に参加された清水目さんと小幡さんの内容を教えてください。昨年は具体的にどのような現場に入り、どんなことをされたのでしょうか?
清水目 : 僕は、家電製品の品質保証に関する現場に入らせてもらいました。そこでは、家電製品の故障に関連するデータが日々集まってくるので、「集計される故障データを有効活用できないか?」という相談からスタートしました。
――「これを解決して」ではなく、「何を解決するか」を考えることがスタート地点なんですね。
清水目 : そうですね。ヒアリング等を進めていくと、現場では機械ではなく人間の感覚で製品故障の増加傾向を判断しており、それに伴い傾向をつかむのが遅れ、対策も遅れるケースがあることが分かりました。
そのような中で、特に新製品の故障件数が膨れ上がる前に早めに検知したい、というニーズがありました。
これに対して議論を重ね、故障データ件数の振る舞いに基づいてアラートを出す、という仕様のアルゴリズムを検討・検証する方針になりました。そこで、「異常度」という指標を用いて、故障件数の異常な増加を検知するツール(異常増加検知ツール)を作成しました。さらに、現場で使いやすいように、属人性を排除した万人が使用できるツールとしました。
――製品故障の改善って、まさに解決すべき課題の一丁目一番地で難しそうですね。
清水目 : まず、「異常とは何か?」というところから考える必要があり、最も難度が高かったと感じます。現場レベルで過去のデータを見ながら議論を重ね、「このときに異常だった」という形で定義を進めていきました。最終的に異常増加検知ツールは、各製品にフィットするよう、ある程度現場の方が自分たちで調整できる仕様にしました。
――本当にどっぷり現場に入るんですね!小幡さんはどんな現場に入られたのですか?
小幡 : 私は「射出成形機」という、プラスチックなどの素材を熱で溶かして金型に流し込んで成形する機械の駆動用の「サーボモータ」の異常検知です。
――サーボモータ。初めて聞きました。
小幡 : ロボットや工作機械など最新の機械で採用されている精密制御用のモータで、射出成形機では金型に素材を押し込むために必要なものです。サーボモータからトルクデータや速度・位置などの細かいデータを取得できるので、そこから異常を検知できないかということです。
射出成形機ではサーボモータの回転トルク・速度をタイミングベルトで減速と同時にトルクを増大させ、連結されたボールネジでその回転運動を直動に変換して成形をしているのですが、そのタイミングベルトが長時間の使用で緩んだりすることがありボールネジ側に伝えるトルクが変わったり反応性が悪くなってしまい成形品質に影響が出てしまいます。
――様々なケースが考えられるんですね。
小幡 : 現場に入ってヒアリングを進め、実際にモノを見るからこそ判明する課題も多く存在します。従来はサービス担当の方が直接ベルトテンションの計測をして保守の要否を判断していたのですが、私はサーボモータのデータを分析することによりベルトテンション状態を検知できるように取り組みました。
このようにデータ分析により機械側の状態や異常の検知ができるようになれば保守保全のスマート化につながると考えています。
入社1年目メンバーのケース(青木さん・森岡さん)
――次は、まさに現在(2022年3月時点)、モノづくり実習に参加されている青木さんと森岡さんについても、入られている現場の概要を教えてください。
青木 : 僕は、企業の業務システムなどで利用されるストレージ工場の製造ラインに入りました。そこにはログをはじめ様々なデータがあるにはあったのですが、分析対象として扱える状態ではありませんでした。なので、まずは「どの工程でどういうデータがあればどんな課題が解決するか」を、現場担当の方が分かるようにお伝えするところからスタートしました。
――分析対象として扱える状態ではないとは、具体的にどういうことですか?
青木 : 例えば10年前に買った装置と昨年買った装置とではデータ形式が違うことがほとんどなので、分析できるようなフォーマットになっていないことが挙げられます。そもそも、別々の装置のデータをマージして分析するというアプローチが今までなされていなかったので、「このデータとこのデータをくっつけるとこんなことができる」ということを、現場担当の方にしっかりとイメージしていただく必要があります。
現場の製造ラインを実際に視認して、どんなデータがあるのか。それを知るためにも最初は、セキュリティの問題で自分たちでは参照ができないものも含めて探っていきました。
――データ変換などが大変そうですね。
青木 : そうですね。今回のお話の背景には、過去に不良率の高かった製品に対して、今は同じテストを3回やっているという工程の存在があります。その3回の工程の全ログのテキストデータをテーブルデータに変換し、全てを見える化して、まずは集計ができるようにしました。担当の方はそれでも満足されていたのですが、僕としてはさらに一歩踏み込んで、機械学習を用いてエラーが起こる際の要因分析を進めていきたいと考えています。
――継続的に進めていかれるということで、すばらしいですね。森岡さんはいかがでしょうか?
森岡 : 自分が今入っている現場は、ホイスト・モートルブロックと呼ばれる、工場などでよく使われる「クレーン」の荷物を持ち上げたり、降ろしたりする動作部分の製造ラインです。
今まで3人がお話しした状況とは異なり、データがなく「製品の異常を検知する」という課題だけがあるという状況でした。ですので、まずはどのようにデータを取得していくのかというところからスタートしました。
――DXを進めるにあたって、そもそもの「使えるデータがない」という話をよく聞きますが、まさにそのパターンということですね。
森岡 : そうですね。まず、データを取るために、実際にラインを流れる製品の画像を撮影していくことにしました。ですが、対象の製品と言っても様々で、500kgのものから5tのものまで複数の製品がラインに流れているので、撮影方法を工夫する必要がありました。遠すぎると画素に対して被写体が小さくなりすぎるのでうまく撮影できませんし、近すぎると必要な情報が全て入りきらず、作業の安全面でも問題がありました。なので、それぞれどういう画角で撮影をするのが良いのかを議論しながら決めていき、その上で1週間ほど製造ラインに張り付いて、画像を取得していきました。
――まさに、現地現物でしか判断できないことですね。
森岡 : そうなんです。取得した画像データを用いて製品の異常検知モデルを構築していくのですが、それには異常データも必要になってくるので、現場の方に相談して、わざと異常がある製品を流していただいたりもしました。
――稼働しているラインでやらせてもらえるって、すごいですね!
森岡 : 本当に、現場の皆さまには多くの点でご協力いただいています。今後は実運用を見据えて、異常検知モデルやトレーサビリティ向上に関するシステム化について検討しているところです。
一番大変なのは「顧客の課題が曖昧だ」ということ
――ここまで、皆さまが入った現場の状況やアクション内容を伺いましたが、そこから得られたことや学びになったことについても、教えてください。
清水目 : 実際に社内のクライアントと話すことで、課題が当初の想定と違っていたり、話を進めていく中であれもこれも課題と積みあがってきたり、ということもありました。そのため、何から着手するかの優先順位付けや、3ヶ月間と時間が限られている中でどのようにアウトプットしていくかを考えること、これらが非常に学びになりました。
――アウトプットで工夫されたことなどはありますか?
清水目 : 現場で触って判断できるものが必要だろうと考え、簡単ではありますがGUIで操作できるものを作って提供しました。結果的に、すごく高評価をいただくことができました。さらに、現場からは「もっとこういうことをやりたい」という声もあがっているので、「IoTデータを活用した故障要因探索システム」という形で、実習を超えて、継続的に開発を進めていくことになっています。
――モノづくり実習が終わっても支援は継続するんですね。
徳永 : この辺りは本人次第といった部分も大きいと思います。現場感として「これは使える!」という形で信頼をしていただけたことが、継続的な開発支援につながっていると思います。
――素晴らしいですね。小幡さんは、学びとしてはいかがですか?
小幡 : LDSLではフロントのビジネスユニットに所属するSEやエンジニアとチームを組んで活動することが多く、直接クライアントと相対しない場合もあります。でも、モノづくり実習では自分で資料を作って現場に行って説明し、課題を持ち帰って分析に活かすという一連のプロセスを体験できる点が非常に良いなと感じました。特に資料作りに関しては、伝え方の難しさを実感しました。
――やはりアウトプットの部分で難易度が高いんですね。資料について、工夫されたのはどんなところなのでしょう?
小幡 : データ分析の結果については統計的な話をしなければいけないのですが、専門的な言葉を用いてもなかなか伝わりません。なので、データの状況をイメージしやすいようにグラフなど視覚的に伝わる工夫をして、一目で分かるようにしました。その結果、「こういうのを知りたかった」と言っていただけたのは嬉しかったですね。
――現在実習中の1年目のおふたりはいかがでしょうか?
青木 : 今まさに実習を進めている中で、いちばん大変だと感じているのが、顧客の課題が曖昧だということです。課題内容がはっきりしていないからこそ、そこを言語化するのにかなり苦労しました。データだけでは何ができるか分からないというクライアントに対しては、とにかく議論を繰り返すことで僕もドメイン知識を身につけていき、課題の仮説を立てながらデータの見える化を進めていきました。
――課題を見つけるのって、ある意味で課題を解決すること以上に難しく、かつ正解がない部分ですからね。
青木 : 特に、僕が入った現場で扱うストレージ製品は、絶対に不良品を外に出さないようにする必要があります。だからこそ、機械学習とオペレーションを組み合わせて、エラーを起こさない設計をする必要がある。まさに今はそこの部分をやっているところですね。
森岡 : 今の話に少し重なりますが、例えば学生時代は整えられたキレイなデータが与えられていました。でも、現場ではそんな良い環境であることは珍しく、実際に撮影をするなどして使えるデータの作成から分析まで一貫して経験できたことは、大きな学びだと感じています。
――森岡さんの場合は、特にそうですよね。実際に足を運ばないと分からないことが多かったと思います。
森岡 : 確かにそうですね。先ほどお伝えした画角や角度の調整などの観点は、データを眺めているだけでは絶対に分からないことでした。最初は「簡単にデータ取得できるだろう」くらいに思っていました。しかし、現場で初めて分かる制約を加味して検討を進めなければならなかったので、その経験も大きな学びになりました。
「モノづくり実習」そのものが喜びになる
――次に、日立製作所でデータサイエンティストとして働く醍醐味ややりがいについて、それぞれ教えてください。
清水目 : モノづくり実習があったこと自体が喜びだし、自慢にもなると感じています。こういった実際の現場での経験ができるところって、そうそうないと思うので。
小幡 : 同じく、現場に入る機会はなかなかないので、そこが特にアドバンテージだと思います。また、日立は様々な領域で事業展開しているので、多様なデータに触れることができるのも良いですね。
青木 : 入社1年目で、あり得ない体験ができたと感じています。あとは、様々なバックグラウンドを持った上司や先輩と一緒に仕事ができることが、とても楽しいですね。例えば徳永さんは工場の話にとても精通されているので、工場にまつわる質問や相談ができます。人の多様性という観点でも面白いと思います。
森岡 : データサイエンティストには大きく2つのタイプがあると思います。ひとつは特定のドメインを掘り下げるタイプ。もうひとつは、横断のテーマに取り組むタイプ。自分自身の入社動機につながる話なのですが、自分は多くのことに興味があるので、日立では幅広い領域でデータサイエンスの仕事ができる点がすごくいいなと思っています。
――この流れで、今後日立製作所でめざしたい「データサイエンティストとしてのキャリア」についても、それぞれ教えてください。
森岡 : 実運用というところで、もっとシステム化までを一気通貫で考えるデータサイエンスをやりたいと考えています。PoC(概念実証)止まりの現場が多い中で、いかにシステム化までつなげ、いかに運用後の部分までを考えられるか。ここが今後の目標になります。
小幡 : データ分析だけではなく、課題を積極的に見つけにいって、将来的には課題を先取りして予防できるようなデータサイエンティストになりたいです。
青木 : ただ分析をするだけではなくて、分析結果を使った企画立案までやりたいですね。そのためにも個人的にKaggleなどにも積極的に挑戦して、解法を共有するなど、より分析の力を高めていきたいと思います。
清水目 : 「課題はここですよね?」と特定できるデータサイエンティストがかっこいいなと思っています。ただの作業者ではなく、データサイエンティストとして様々な情報や人をつなげて、DXを推進できるような存在になりたいです。
徳永 : データサイエンスには、必ず「顧客に価値を提供する」ための翻訳が必要になります。社会課題を解決することが我々のミッションなので、単に「分析に強い」だけではなく、そこまでしっかりと考えて手を動かせる人財になってもらいたいですね。
日立では、自分の強みを活かせるチームがきっと組めるはず
――それでは最後に、読者の皆さまにメッセージをお願いします。
清水目 : 「面白いことを真剣にできる」いたずら好きな人と一緒に仕事をしたいと思っています。ぜひ日立で一緒にデータサイエンス領域を高めていきましょう。
小幡 : 今回のテーマである「モノづくり実習」然り、日立では新人のうちから意見がとても尊重される環境なので、そこがすごいと感じています。軸をもっている人にとっては、やりたいことがしやすい環境だと思うので、そういう人にはぜひ来ていただけるといいなと思います。
青木 : 僕は、業務に限らず分析コンペも好きなので、プライベートでも分析が好きな人と一緒に挑戦できたらいいなと思っています!
森岡 : 日立には様々な能力を持った人がいるので、自分の強みを活かせるチームがきっと組めるはずです。何かしらの社会課題を解決したいという人にはとても良い環境だと思います。
徳永 : ぜひ、熱意をもって仕事ができる人に来てほしいですよね。私は、「優れた自主技術・製品の開発を通じて社会に貢献する」という日立の企業理念に深く共感しています。だからこそ、データサイエンスの力を使って、一緒に社会課題を解決できるような仕事ができたらなと思っています。
編集後記
今回の対談インタビューでは、非常に多くの「モノづくり現場」のお話を伺うことができました。工場萌えの自分としては、非常に興奮する時間でした。
特にすごいなと思ったのが、入社1年目から実際にラインを止めてまで必要なデータの作成をさせてもらえるということ。2020年に立ち上がったLumada Data Science Lab.が、独立した一部門ではなく、会社全体の仕組みにしっかりと浸透していることが改めて分かる内容だと感じました。
なお、Lumada Data Science Lab.については以下の記事でも詳細に語られているので(徳永様も出演しています)、こちらも併せてご覧ください。
日立が組織するデータサイエンス「特殊部隊」とは?トップデータサイエンティストを結集したLumada Data Science Lab.に迫る。
取材/文:長岡武司
撮影:平舘平
「Qiita×HITACHI」AI/データ×社会課題解決 コラボレーションサイト公開中!
「Qiita×HITACHI」AI/データ×社会課題解決 コラボレーションサイト公開中!
日立製作所の最新技術情報や取り組み事例などを紹介しています
コラボレーションサイトへ
日立製作所経験者採用実施中!
AI/アナリティクス技術により顧客の課題解決を行うデータサイエンティスト
[Assistant Manager]
募集職種詳細はこちら
日立製作所の人とキャリアに関するコンテンツを発信中!
デジタルで社会の課題を解決する日立製作所の人とキャリアを知ることができます
Hitachi’s Digital Careersはこちら