業務プロセスに着目したデジタルツインで製造業DXを加速!日立のデータハンドリング技術がもたらす未来とは
日本の屋台骨を支える製造業は、長年のオペレーションを通じて非常に効率的な工程管理を実現しています。一方で、せっかくの現場データを有効活用できていないという課題を業界全体で抱えています。
今回は、そんな製造業のDXを推進するためのソリューションを展開している日立製作所のデータハンドリング技術について取材しました。中でも、業務のプロセスに着目し、デジタルツインによるデータの可視化を可能にする「IoTコンパス」と呼ばれるソリューションは、現場からの引き合いが非常に多く、様々な企業に導入されていると言います。
デジタルツインとはどのようなもので、どのような思想のもとで構築されているのか。様々な案件のDXに携わるエンジニア3名にお話を伺いました。
日立製作所経験者採用実施中!
素材産業を中心とした製造業向けにDX・AI事業を牽引するプロジェクトマネージャー/リーダー
募集職種詳細はこちら
目次
プロフィール
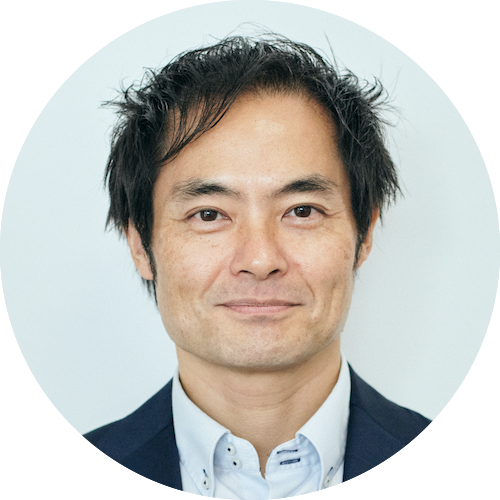
サービス&プラットフォームビジネスユニット アプリケーションサービス事業部 Lumadaソリューション推進本部 アプリケーション開発部 主任技師
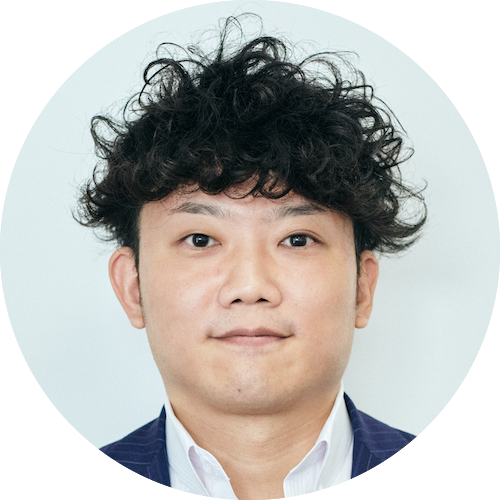
インダストリアルデジタルビジネスユニット デジタルソリューション事業統括本部 ソリューション&サービス事業部 産業IT第2ソリューション部 主任技師
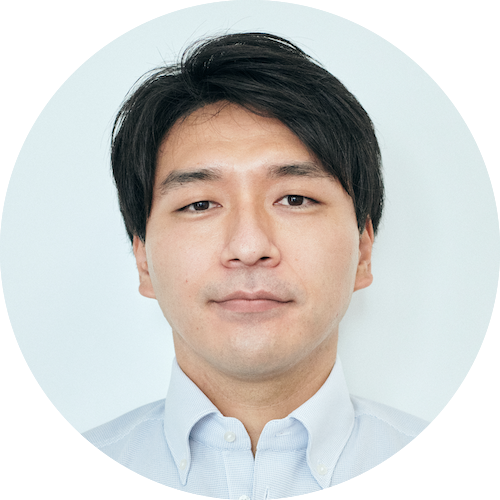
インダストリアルデジタルビジネスユニット トータルシームレスソリューション統括本部 技術戦略本部 協創・アーキテクチャ推進部 技師
ITとOTをつなげる日立のDXソリューション群
――まずは日立のDXソリューションの全体像について教えてください。
上木 : 日立が策定・提唱している生産システムの「成熟度モデル(Maturity Model)」では、DXの成熟度を「6段階」に分けて設定しています。レベル1はデータを収集・見える化するフェーズです。そこからレベル2・3・4と上がっていくにつれて、収集したデータをどのように価値あるデータにし、現場管理を高度化していくかを定めています。そして最終的にはレベル5・6で、生産計画やサプライチェーンの最適化につなげていきます。レベルの段階を追うことでより高度なDXを推進できる、という考え方のもとでお客さまをご支援しています。
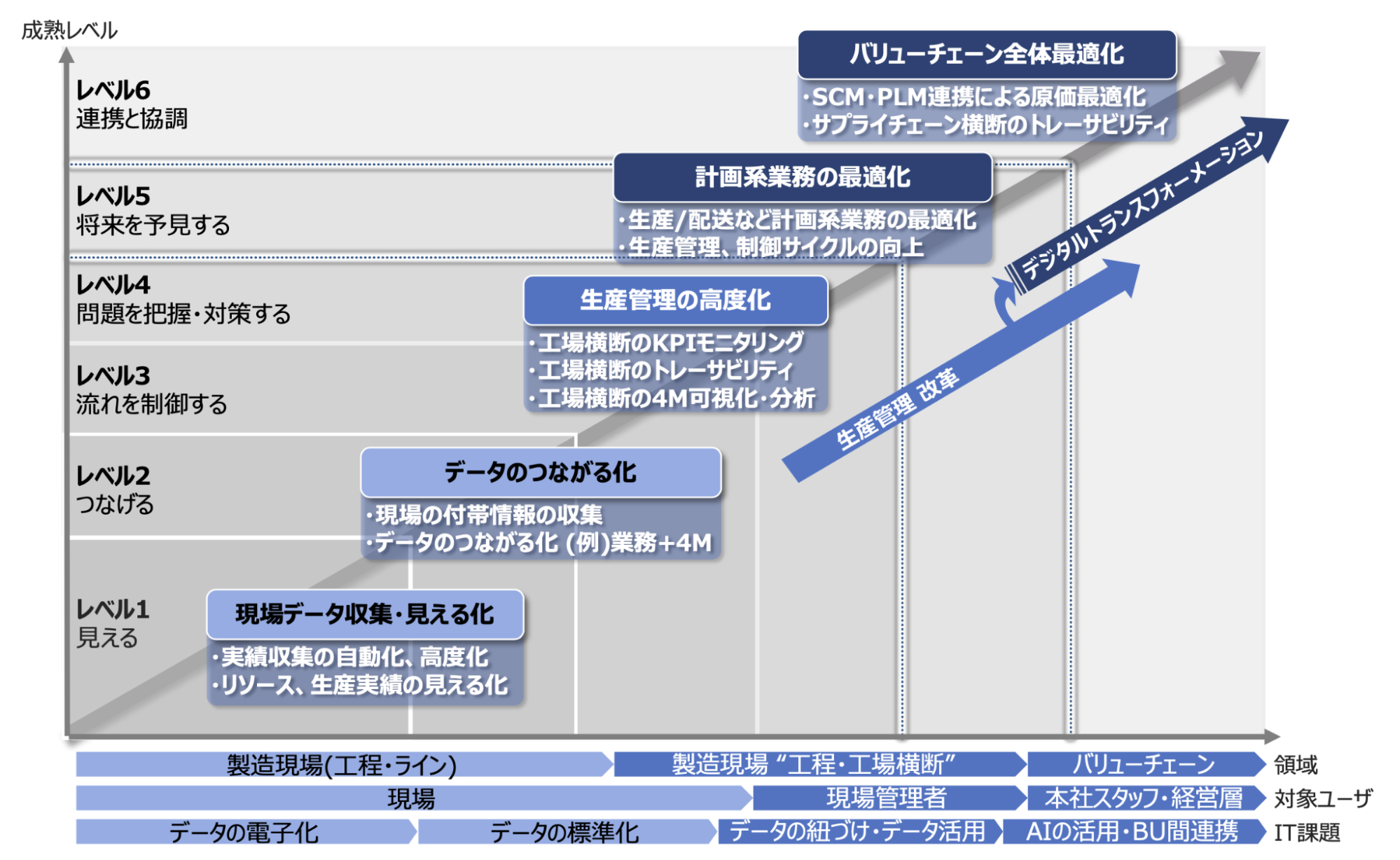
日立が策定・提唱している生産システムの「成熟度モデル」をベースに、現状把握から「目的/めざす領域」の設定、目的に応じた段階的な成熟レベルの向上まで、各段階に応じたDX推進を支援している
上木 : 昨今のお客さまの状況に鑑みると、現場の設備(OT:Operational Technology)は充実していますし、ERPを代表とする経営システムなども十分に導入されています。一方で、これら領域のはざまに目を向けると、つなぐDXソリューションの導入はまだまだこれからというお客さまの声が多くあり、ご期待に応えるため力を入れています。
――例えば現場デバイスとERPをつなげるとなると、細かいつなぎこみが必要だと感じるのですが、具体的にはどのように設計されているのでしょうか?
上木 : 具体的にはこの間を細かくレイヤー0〜4の5段階に分け、それぞれについて個別のソリューションを設定しています。ざっくりとお伝えすると、レイヤー0・1は実際の設備に紐づいたデータを収集する部分で、レイヤー2・3はそれらのデータを事業的に価値あるものへと見える化する部分となります。そして最終的にはレイヤー4で、それらのデータをERPや各種基幹システムへとフィードバックするということを掲げています。
上木 : 特に我々が注力しているのはレイヤー2・3の部分です。例えば製造計画の見直しや、製造実行系のMES(製造実行システム)の部分など、お客さまが定めている各種KPIの達成をサポートするために、それぞれ「際」となる課題をワンストップで解決する「トータルシームレスソリューション」をご提案しています。
お客さまの課題は千差万別
――今ご説明があったDXソリューションの提供にあたって、皆さまの役割分担を教えてください。
阿部 : 私は、製造業であれば「どのようなスマートファクトリーの構想を描いていくか」「将来的に何をめざすのか」など、お客さまにご相談内容を伺うところから一緒に伴走させていただいています。
お客さまから最初にご相談いただく内容は、現場のオペレーションなどに根差したものが多いのですが、「俯瞰した目線で見たときにどういう課題があるのかをデザインしていく」というアプローチをとることが多いです。
――阿部さんは上流のグランドデザインなどを担当されているということですね。
阿部 : はい。ある程度の方向性が固まったら、そこから個別具体的なデータを抽出していき、上木さんをはじめとするフロントSEの方々と協力して、より具体的なシステム設計へと落とし込んでいきます。その際に、導入するプロダクトのエンジニアにもジョインしていただき、一緒にプロジェクトを進めていくことになります。
例えば、DXソリューションの中でも特に引き合いが強い「IoTコンパス」の導入については、古橋さんをはじめとするエンジニアの方々に入っていただいています。
――先ほどの0〜4レイヤーの図で複数のDXソリューションがマッピングされていましたが、その中でも「IoTコンパス」が特に引き合いが強いんですね。
阿部 : もちろん、お客さまが抱えている課題によってはそうでないこともありますが、生産工程全体を「プロセス」の観点で可視化するツールとして、多くのプロジェクトにおいて重要な位置付けのソリューションとなっていますね。
――なるほど。私自身、生産現場に入ったことがないのですが、具体的にお客さまはどのようなことにお困りなのでしょうか?
上木 : お客さまが抱える課題は千差万別です。業務に紙や電話を使っていて、データのデジタル化から必要なケースもあれば、データ収集は出来ているもののそれらをどのようにつなげて活用すれば良いのか分からないというケースもあります。
――そもそも、お客さま自身は課題を認識されているものなのか、そこも一緒に探していくものなのか。どちらのケースが多いのでしょうか?
上木 : そこもバラバラでして、「こういう観点で分析をしたい」という明確なポリシーをもっているお客さまもいれば、「そもそもどのような観点でデータを見たらいいのか分からない」という相談ベースでいらっしゃるお客さまもいます。現在は前者のお客さまが多いのですが、どちらのケースにおいてもこれまで培ってきたノウハウや過去の事例をお伝えしながら、提案型でコミュニケーションをするようにしています。
現場活動をプロセスでデジタルツインにする「IoTコンパス」
――先ほどお話に出てきた「IoTコンパス」について、ソリューションの概要を教えてください。
古橋 : IoTコンパスは、工場などにある各工程のデータを集約して、一種のデジタルツインとしてプロセスを再現していくソリューションになります。
工場という場所は多くのケースで閉じられた世界になっており、現場はかなり細分化されていて隣の現場のことは全くわからないということが往々にしてあります。
そういった状況の中で、複数の現場を紐づけて工程横断で最適化しようとすると、どのデータを取ってくるべきなのかが分からないといった声や、そもそものデータの意味が分からないなどの課題が発生します。それらを解決するのが、現場活動を「プロセス」でデジタルツインにするIoTコンパスというソリューションです。
――プロセスでデジタルツインにする、とはどういうことでしょうか?
古橋 : こちらの図では、「リアルな世界」として下段にお客さまの工場の様子が描かれています。デジタルツインは、上段のように、行われている操業に関わる情報をデジタル空間で整理・再現することで、製品の品質など様々なものを可視化することができます。
古橋 : IoTコンパスは、このように「4Mデータ*¹が密接に紐づいていて、かつ工場の生産が業務の繰り返しによって成立している」ということに着目して設計されたもので、「4M+業務」のデータを抽出してリアルな世界を投射します。一般的に言われるデジタルツインは「モノ視点」で設計されることが多いと思うのですが、IoTコンパスは「業務視点」ということで、プロセスの流れをデジタルツインにするという部分が大きな特徴になっています。
*¹ 4M:huMan(人・作業者)、Machine(設備・機械)、Material(材料・部品)、Method(方法・作業手順)
――なるほど。設備や生産物といったモノではなく、業務というプロセスを軸に考えているということなんですね。
古橋 : 工場の各ラインでもサプライチェーンでも、中心には必ず何かしらの業務があり、そこに部品が流れてきてマシンや作業者、作業手順が加わることで完成品が作られていくことになります。この「4M+業務」を複数つなげていくことで工場の工程やサプライチェーンが再現できる、という考えのもとで設計されています。
古橋 : IoTコンパスでは、それぞれの4Mデータが実際の現場のどこに紐づいているのかという情報をグラフ構造として持っているので、それを辿っていくことで、完成品の製造時のデータ状況や条件、作業担当者、当時行われた手順などを取り出すことができます。
品質向上からCO2排出量モニタリングまで、幅広い用途で活躍
――業務にも様々な種類があると思うのですが、粒度としてはどのようなものになるのでしょうか?
古橋 : こちらの図は、ある消費材メーカーにおける工程をサンプルとして可視化したものになります。「包装容器を成型し、その中に商品を充填して出荷する」という仮定の工程を表したもので、青い丸で表現したものがそれぞれ業務+4Mデータの塊になります。
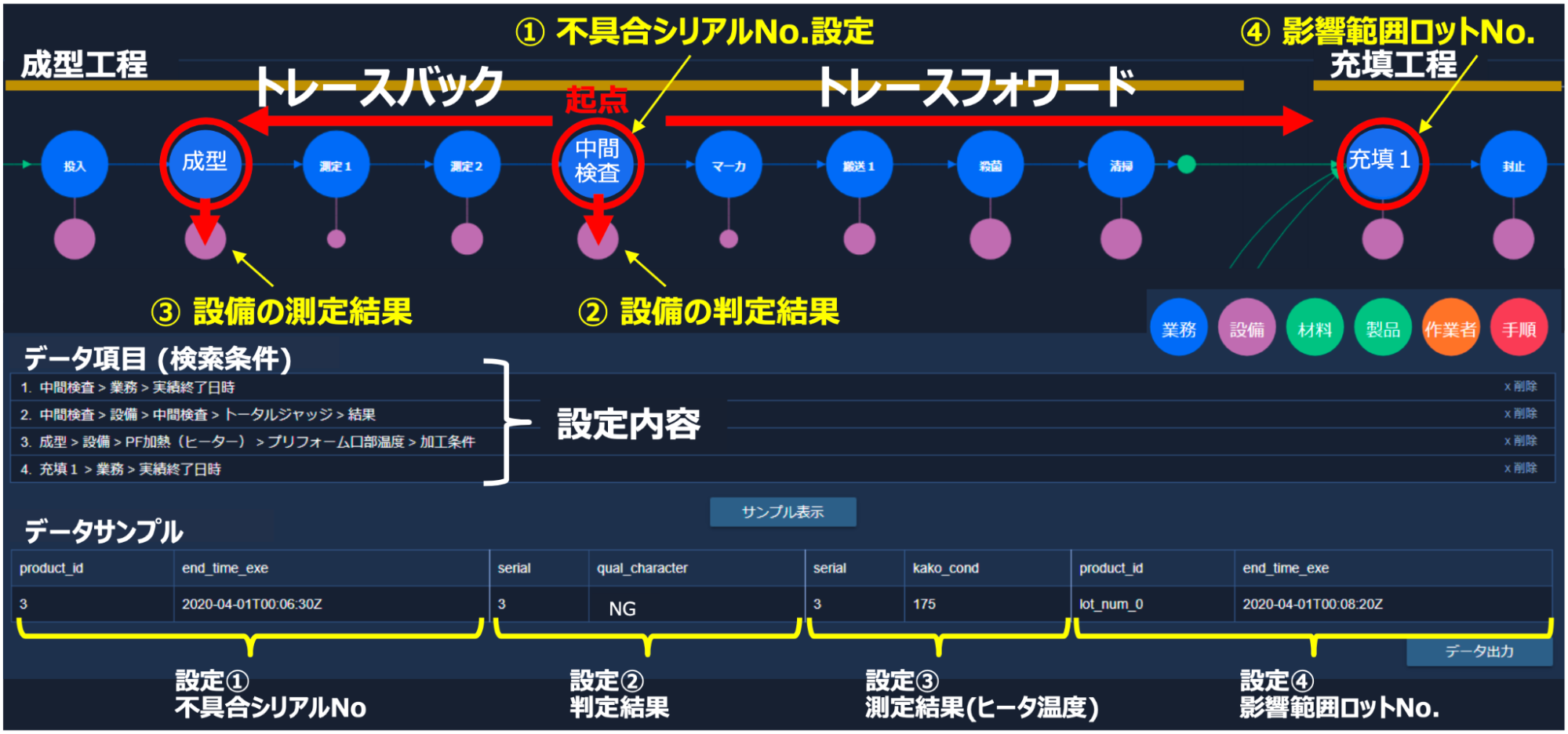
「成型」と表示されているところで、プラスチックの塊から包装容器をつくる業務が表現されている。その後、検査(「中間検査」と表示)を経てマーカ等をつけた後に、「充填」と表示されているところで商品が入り、「封止」の部分で容器を閉じるという工程が表現されている
――こうやって見てみると、表現されている業務工程の単位は想像以上に大きいと感じます。「容器を閉じる」ような、より細かい単位かと思っていました。
古橋 : 工場のラインをイメージしていただくと分かりやすいと思うのですが、よく工場で「着完」と表現される、部品(Material)が到着して工程が完了するまでのプロセスの中には、複数の作業が入り込んでいます。一つひとつの細かい作業を単位にするのではなく、工程の着完をひとつの業務として管理をするという考え方です。
阿部 : もちろん、自動車のような組立製造*²の場合は、もっと多くの業務に分解できると思います。ここで設定する業務の単位については、最小の作業をある程度まとめた「ユニット」の単位で表現することが多いのですが、例えば100あるものを50にしたり30にしたりと、いかようにもカスタムできるので、お客さまの状況や実現したいことによって青丸の数は変わってきます。
上木 : 組立製造に比べると、プロセス製造*³はある程度大きなくくりで業務を集約できるので、数としては10数個の範囲におさまる傾向がありますね。IoTコンパスはもともと組立製造を前提にソリューション開発をスタートしたのですが、次第にプロセス製造でのニーズも多くあることがわかってきたので、そのような機能に最適化していった背景があります。
*² *³ 組立製造とは、電子機器や精密機械のような部品や材料を組み立てて完成品を生産する製造のことを指す。一方でプロセス製造とは、化学や医薬、鋼鉄、食品など、流体を原材料とし、化学反応により付加価値を向上させる製造のことを指す。
――なるほど。このように業務プロセスを可視化したものを、具体的にどう使うのでしょうか?
古橋 : 例えば中間検査工程で何か不具合が見つかった場合、まずはどのような条件で該当の不具合が発生しているのかを調べ、同時にその影響範囲を明らかにする必要があります。
前者については、成型をしたときの温度を調べていくなど、トレースバック(製品から部品・材料ロットの特定)をしていくことになります。そこで、誤った温度となっていたタイミングが特定できたとすると、そのプロセスの周辺で処理された容器にも同様の不具合があることが想定されます。そうやって、どの段ボールに入ってどの出荷先へと運ばれたかまでをトレースフォワード(部品・材料ロットから影響する製品範囲の探査)することになります。
このようなトレースバック・トレースフォワードの実施を容易にして、迅速かつ適正なリコール範囲を特定できるようになる点が、IoTコンパス導入の大きなメリットのひとつになります。もちろん、品質の向上にも大きく寄与すると考えています。
上木 : 他にも、トレーサビリティを応用して、カーボンニュートラルに向けたCO2排出量のモニタリングとして活用されるケースもあります。作る工程で発生するCO2排出量はもちろん、そのための電気を発電するための排出量、調達した部品一つひとつを作るときの排出量、そして製品を使う際の排出量など、製品のライフサイクル全体におけるCO2排出量の確認としてもご活用いただけます。
――データドリブンなトレーサビリティが実現すると、活用の幅が広がるということですね。ちなみに、お客さまごとにこれらの業務を可視化しようとすると毎回時間がかかると思うのですが、その辺りの負荷はどうコントロールされているのでしょうか?
古橋 : 例えばPCBA(プリント回路基板アセンブリ)の工程については、EMS(電子機器の受託生産)が盛んであることに鑑みても、ある程度工程が標準化されています。つまり、先ほどご覧いただいた青い丸の並びが、ある程度同じであることが多いので、そのような標準化がなされている工程については製造モデルのテンプレート化を進めています。
また、標準APIをサポートすることでアプリケーション開発のスピードアップも進めるようにしています。
工場を超えたサプライチェーン全体の最適化にもチャレンジ中
――ここまで教えていただいた「IoTコンパス」をはじめ、皆さまが携わっているDXソリューションの提供を通じて、めざされているゴールについて教えてください。
古橋 : 製造業に限った話ではありませんが、少子高齢化や技術承継などの大きな課題への対策を考えていく必要があるからこそ、工場の業務を効率化して生産性を上げていかねばならないと感じています。そのためのソリューションとしてどんどん活用していただきたいです。
また、人々の嗜好の多様化に伴う「多品種少量生産」のトレンドも無視できません。「たくさん作れば良い」という時代から一変して、「求められたものを必要な数だけ生産する」ということが要求されるようになるので、より難度が高い世界になると想像しています。
大きく急激な変化が求められる時代において効率化を進めるためには、データを「分かる形」で取り出して分析を進める必要があるわけで、そのためのツールとしても活用していただきたいと考えています。
――製造業における工場以外での活用としてはいかがでしょうか?
阿部 : サプライチェーン全体も同じような状況に陥っているので、そこをつなげることでさらに広範な全体最適を実現できないかという観点で取り組みを進めています。特に昨今ではコロナ禍による調達難の流れがあるので、プロセス全体で最適化しないことには問題解決につながらないことも多くなっていると感じます。
また、サプライチェーン全体で考えるとトップダウンじゃないとうまく進みませんし、スケジュール感としても中期経営計画のスパンで捉える必要があります。
――DXはここ数年で随分と必要性が叫ばれるようになりましたが、実際にお客さまに変化はありますか?
上木 : 「DXをやらねばならない」という意識は明確にお持ちなのですが、何から手をつければ良いのか分からない、実際に自社の中でどこまでやれているのかが分からない、といったお客さまは多いです。システムを作るにしても、中長期的な目標を作ってからでないと本質的な効果につながりません。ソリューションありきではなく、まずはしっかりと目標を定めて、実現するためのひとつの手段として様々なソリューションの中から最適なものを選択して目標達成していくという部分を一緒に考えるようにしています。
日立には、社内に新しいトライアルの場がたくさんある
――皆さまのキャリアと日立製作所というフィールドについても教えてください。まずは、今後日立でめざしたいことやキャリアについて、それぞれ教えてください。
阿部 : 私はエンジニアとして入社して、2016年のDXソリューション部隊への異動をきっかけに、徐々に業務の中で戦略コンサルティングが求められていくようになりました。これが自分にすごく合っているなと思っています。ただ「システムを作ります」という時代ではなくなっているからこそ、テクノロジーをコアに置きながら業務や事業戦略に関わるストラテジストとしてのキャリアを歩みたいと思っています。
上木 : 私は産業系SEとして一通りの経験をしてきたのですが、まだ周囲の経験やノウハウが十分に揃っていない未知の領域(DX、IoT)にチャレンジしたいという思いを常に持っていました。先ほど阿部さんがおっしゃった通り、お客さまを取り巻く環境が大きく変わっている状況だからこそ、引き続きこの領域での知見を溜めてお客さまにフィードバックしていきたいと考えています。
古橋 : もともとサーバー、ストレージやネットワーク関係のことをやっていたこともあって、データについてはこだわりがありますし、データ視点でお客さまと話すことで初めて分かることがたくさんあります。そのプロセスの中で、改めて日立の強みを感じているからこそ、業務の最適化につながる提案をどんどんしていきたいなと思います。
――いま「日立の強み」と表現されましたが、皆さまが感じる日立の強みはどのようなところでしょうか?
上木 : やりたい仕事を実際にやれるというところですね。当然、意思表示と実績は必要になりますが、一つひとつの事業は大きいものから小さいものまで多岐にわたるので、それに応じてチャンスもたくさんあります。
古橋 : 今のお話に付随して、様々な人がいることが強みだと思います。製造設備からERP、人財管理システムまで様々な事業領域があって、それぞれのエキスパートが社内に揃っています。そして困ったときに相談をすると、皆さん快く応えてくれます。日立の社員は誠実で真面目な人が多いので、積極的に連携をしていくことでより価値あるものを提供できると日々実感しています。
阿部 : あとは、社内に新しいトライアルの場がたくさんあることもありがたいですね。古橋さんがおっしゃる通り、事業領域が多岐にわたるので、グループ会社含めて先進的なことを試せる機会が多くあることは、新規事業を作る上で大きなアドバンテージだと感じます。
――ありがとうございます。それでは最後に、読者の皆さまに一言ずつメッセージをお願いします!
阿部 : 私のキャリアがエンジニアからコンサルタントへと広がっていったように、その人の志向性に併せたキャリア展開をしやすい会社だと思うので、ぜひチャレンジ精神旺盛な方に来ていただければと思っています。
上木 : 今は多様性の世の中ですから、ご自身の軸となる技術やスキルをしっかりと確立された上で、ぜひ様々なことにチャレンジしていただけたらと思います。
古橋 : 日立はITにもOTにも非常に強い会社だと思っています。また、実際に今起きている課題を解決していくという観点でも国内有数の会社だと思うので、IT × OT領域に興味のある人はぜひ入社していただきたいと思います!
編集後記
今回取材をして感じたのは、お話を伺った3名のコミュニケーションが非常になめらかで、チーム連携がとてもうまくいっているだろうなということです。私自身、DXのような複雑な問題解決への提案および導入活動においては、プロダクトの完成度はもとよりチームメンバー同士の円滑で率直なコミュニケーションが不可欠だと感じているからこそ、今回のチームは非常にうまく機能されているんだろうなと感じた次第です。製造業という、日本経済の要を支える重要なミッションを担う存在として、非常にテンションの上がる取材となりました。
取材/文:長岡武司
撮影:平舘平
「Qiita×HITACHI」AI/データ×社会課題解決 コラボレーションサイト公開中!
「Qiita×HITACHI」AI/データ×社会課題解決 コラボレーションサイト公開中!
日立製作所の最新技術情報や取り組み事例などを紹介しています
コラボレーションサイトへ
日立製作所経験者採用実施中!
素材産業を中心とした製造業向けにDX・AI事業を牽引するプロジェクトマネージャー/リーダー
募集職種詳細はこちら
日立製作所の人とキャリアに関するコンテンツを発信中!
デジタルで社会の課題を解決する日立製作所の人とキャリアを知ることができます
Hitachi’s Digital Careersはこちら